Pour une inspection visuelle ou une détection de défauts après dissection, les stomates ont une surface lisse et une forme circulaire.
Cause :
1. La direction d'introduction de l'aluminium en fusion est déraisonnable ou la vitesse d'écoulement du métal en fusion est trop élevée, ce qui entraîne des projections ;
2. Blocage prématuré du conduit d'échappement ou de la paroi d'impact frontal pour former un vortex pour envelopper l'air, de tels pores produisent souvent des zones d'échappement pauvres ou des cavités profondes ;
3. Parce que la charge n'est pas propre ou que la température de fusion est trop élevée, plus de gaz dans le métal fondu n'est pas éliminé et la précipitation ne peut pas être complètement évacuée pendant la solidification.
4. L'agent de démoulage contient une grande quantité de gaz ou est trop utilisé, et il n'est pas versé avant le versement afin que le gaz soit impliqué dans la coulée et que les pores aient pour la plupart une surface gris foncé;
5. Le point de commutation à grande vitesse est incorrect, la pression est trop basse et l'ouverture d'écoulement est trop petite.
Mesures d'amélioration (prémisse : pas de matériel volant pendant l'injection)
1. Utilisez une charge propre, contrôlez la température de fusion et effectuez un traitement de dégazage ;
2. Sélectionnez des paramètres de processus raisonnables, la vitesse d'injection, le point de commutation à grande vitesse, la pression de stockage d'énergie, la force d'injection, l'ouverture du débit, etc. ;
3. Guidez la balance liquide métallique, remplissez la cavité de manière ordonnée et facilitez l'évacuation du gaz. Il est nécessaire d'améliorer le coureur;
4. La fente d'échappement et la fente de trop-plein doivent avoir une capacité d'échappement suffisante et, si nécessaire, augmenter ou agrandir le sac de scories et la fente d'échappement ;
5. Sélectionnez un agent de démoulage avec une petite quantité d'air et contrôlez le volume d'air.
Rétrécissement
1. Détection anatomique ou de défaut, la cavité est de forme irrégulière, non lisse et la surface est sombre.
2. Les pores de retrait grands et concentrés sont petits et dispersés sous forme de porosité de retrait.
Cause :
1. Pendant le processus de solidification de la coulée, en raison du retrait, le métal liquide ne peut pas être compensé, ce qui entraîne des cavités ;
2. La température de coulée est trop élevée et la distribution du gradient de température du moule est déraisonnable.
3. Le rapport d'injection est faible et la pression de suralimentation est trop faible ;
4. La porte intérieure est mince, la zone est trop petite et se solidifie prématurément, ce qui n'est pas propice à la transmission de pression et à l'alimentation en métal liquide.
5. Il y a des points chauds sur la structure de coulée ou la zone de section change radicalement ;
6. La quantité de coulée de métal fondu est trop petite et le matériau restant est trop mince pour que l'effet d'alimentation ne puisse pas être atteint.
Les mesures d'amélioration
1. Réduisez la température de coulée et réduisez le retrait;
2. Augmentez la pression spécifique d'injection et augmentez la pression pour améliorer la compacité;
3. Modifier la porte intérieure pour améliorer le transfert de pression, ce qui est bénéfique pour l'effet d'alimentation en métal liquide ;
4. Modifiez la structure du moulage, éliminez la partie d'accumulation du moulage et rendez l'épaisseur de paroi aussi uniforme que possible.
5. Accélérez le refroidissement des pièces épaisses et volumineuses;
6. Épaississez la poignée pour augmenter l'effet d'alimentation.
Trou de scories
Il y a des particules métalliques et non métalliques dans le moulage sous pression qui sont différentes de leurs propres matériaux, et leurs positions ne sont pas fixes. Ils ne sont pas faciles à trouver lors de l'inspection aux rayons X et ne peuvent être vus que sur la surface usinée.
Cause :
1. Mélange de scories :
1) Le revêtement du four de fusion, de l'emballage de transfert et du four de maintien tombe ;
2) Après affinage dans le four de fusion, le décrassage n'est pas terminé avant la sortie du four ;
3) L'écume de surface n'est pas éliminée après dégazage dans l'emballage de transfert ;
4) Lorsque le liquide d'alliage est versé dans le four de maintien, la rainure de dérivation n'est ni propre ni filtrée ;
5) Lors de la coulée, le laitier fondu sur la surface liquide du four de maintien n'est pas retiré et pénètre dans la chambre de pression avec la cuillère à verser.
2. Mélange graphite :
1) Le bord du creuset en graphite est tombé et est entré dans l'alliage ;
2) Trop de graphite dans l'agent de démoulage.
Les mesures d'amélioration
1. Utilisez les méthodes suivantes pour empêcher autant que possible les scories de pénétrer dans la cavité
1) Réparez le four ou remplacez le revêtement du four à temps ;
2) Le four de fusion doit scories pour terminer et nettoyer à temps selon les exigences du processus ;
3) Une fois le sac de transfert dégazé, l'écume à la surface doit être nettoyée ;
4) Pour s'assurer que la rainure de déviation est propre, un dispositif de filtrage doit être installé à l'extrémité avant ;
5) Nettoyez l'écume sur la surface liquide du four de maintien. Lorsque vous prélevez le liquide d'alliage avec une cuillère, retirez-le autant que possible de la surface du liquide ;
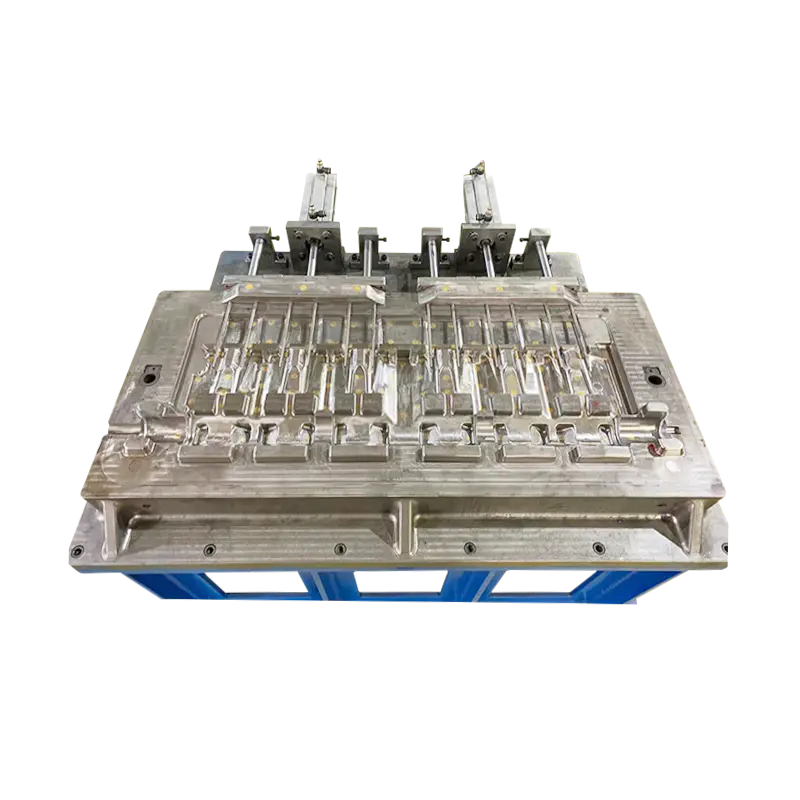